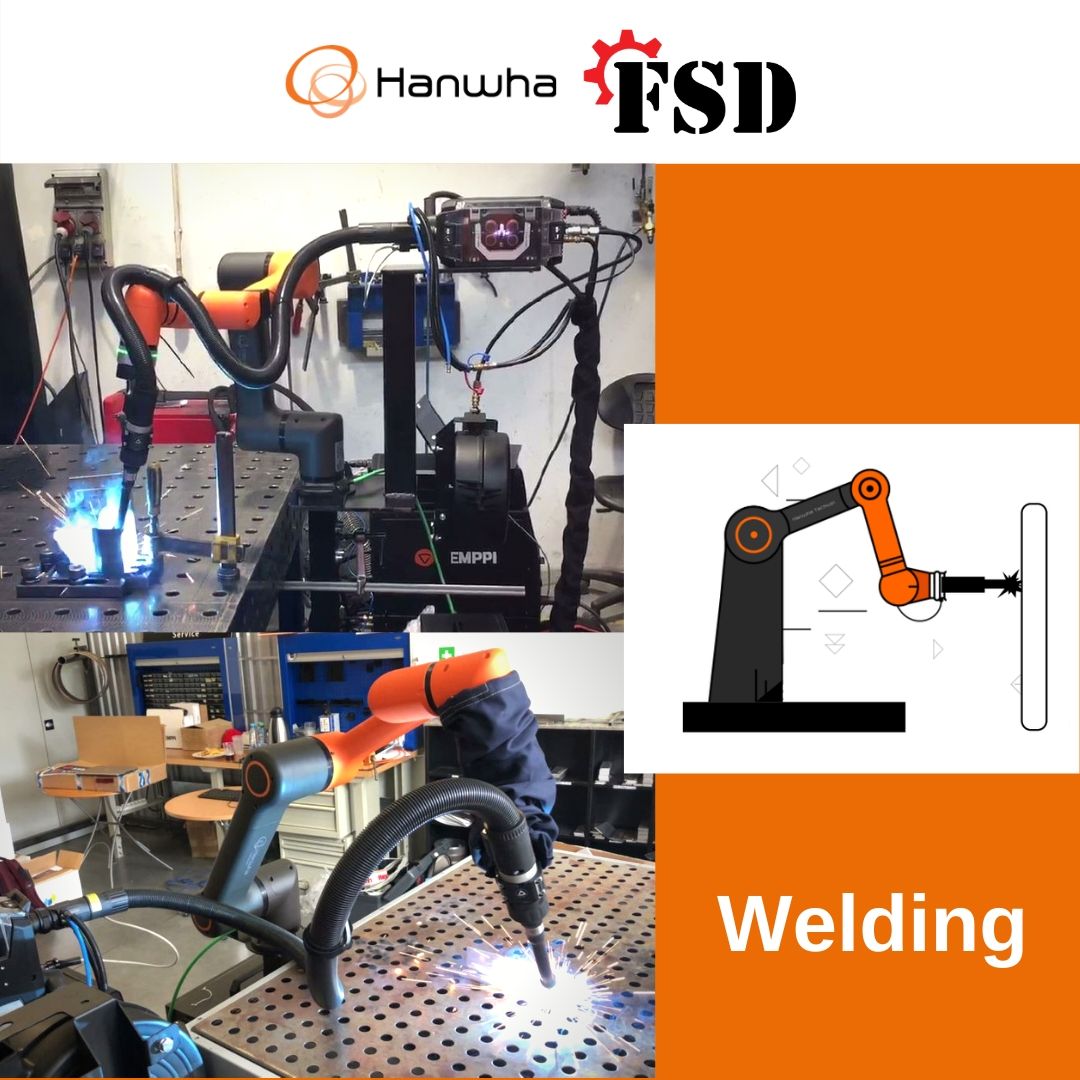
Why Weld With a Hanwha Cobot?
In today’s industrial landscape, adding capacity to robotic welding processes is crucial to optimizing operations that can effectively manage and fulfill the uptick in consumer product variety – sometimes regardless of product volume. To gain the flexibility and capability needed for this, a growing number of manufacturers are implementing collaborative welding robots. A style of flexible automation that can be easily deployed or redeployed on demand, collaborative welding offers some attractive benefits to manufacturers such as:
Quick & Easy to Teach
Collaborative robots, like the Hanwha HCR-12, allow someone familiar with the welding process to hand guide the robot, manually moving the arm and torch through a program path to weld a part. This easy-to-use feature enables manufacturers to train someone unfamiliar with robotics how to use a robot in a matter of minutes, as opposed to hours or days.
Safe
While it is true that a collaborative robot enables a human to safely work with or in close proximity to robots, manufacturers must take the proper precautions. There are already risks associated with any kind of welding including arc flash, weld spatter, hot parts, sharp wire and working with a high current of electricity, regardless of the robot or human manipulation. Keep in mind, collaborative welding is only as safe as all precautions taken while using the hanwha cobot in a welding environment. For this reason, personal protective equipment (PPE) and training is still required, as determined by a thorough risk assessment of the robot, end-of-arm tooling, the workpiece and the robot work area.
Easy to Relocate
Unlike some larger and heavier industrial welding robots that weigh around 150 kg, collaborative robots such as the HCR-12 – weighing in at just 53 kg.
Cobots can even be reinstalled elsewhere within the factory as production needs change. An ideal use for a robot of this nature would be a factory or job shop that already has welding tables set up for humans, where the collaborative robot could easily be wheeled up to help supplement manual labor.
Accommodates High-Mix, Low-Volume Production
The fact that these robots are easy to teach makes them well-suited for high-mix, low-volume production runs. Instead of spending an hour or more programming for a part that only requires a quantity of 50, the person programming an easy-to-use collaborative robot may only need a few minutes before the robot is up and running, allowing for fast changeover. The use of robotic welding for fast-paced production in low quantities also helps to reduce cycle time and maintain quality, while possibly freeing a human worker to perform other value-added tasks or complex welds that sometimes are more suited for a skilled welder rather than a robot.
Lowers Cost per Part
If manual workers are redeployed to other operational duties such as custom welding, there is the opportunity to lower cost per part. If a collaborative robot is running simultaneously while a skilled welder is working on another task, there is great potential to get the average dollar per part down over time, especially after return on investment (ROI) has been achieved.
Welds Longer Continuous Seams
Quality in today’s marketplace is essential, especially for high-mix, low-volume production runs. The use of collaborative welding robots enables the ability to create a longer, continuous weld seam. A skilled welder can only weld about a two-foot seam in a continuous motion, while a cobot can make up to a four-foot seam. This is helpful with long parts, as there can be fewer starts and stops, producing a higher quality weld. This type of part would also typically require a larger welding cell with a lot of dedicated floor space, where a collaborative robot can be pushed into place at the part’s current location.
Other Collaborative Welding Robot Applications
A huge advantage of collaborative robots is the versatility that they can provide. Aside from welding, cobots can also be used for other applications in a welding environment such as loading/unloading a spot ped welder, loading/unloading a standard welding workcell, part and weld seam inspection, post-weld part placing into containers, and part picking and placing.
Is a Collaborative Robot Right for Your Welding Application?
If you’re interested in learning more about adding capacity to your robotic welding processes, Contact us for more information and demos!
Source: https://www.motoman.com/en-us/about/y-blog/collaborative-welding-benefits