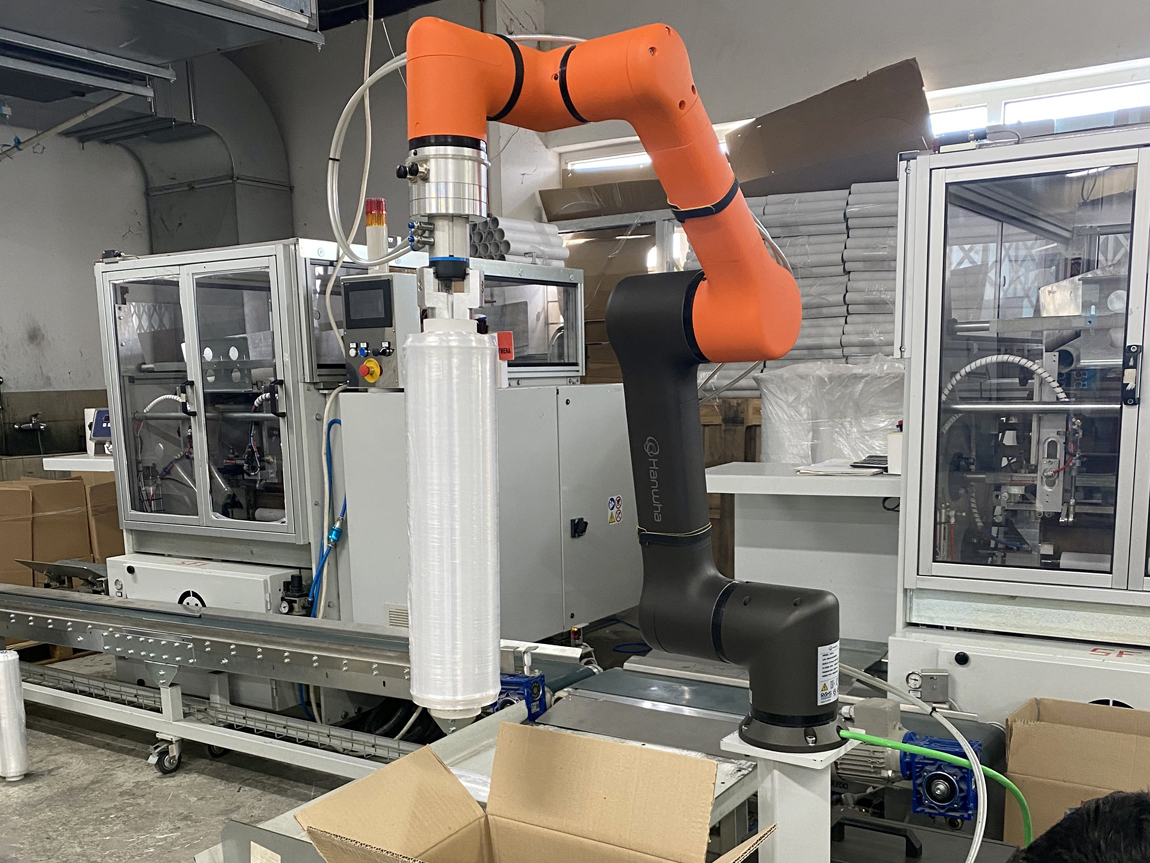
How to capitalize on Cobots in post-COVID industry
Collaborative Robots are increasingly altering the factory floor and business strategy.
COVID-19 has harshly impacted many industries, and industrial manufacturing has proven to be one of them as 80% of manufacturers expect the pandemic to have a financial impact on their business and a majority of those in the sector believe the pandemic will affect operations. Due to the onset of challenges over the past six months, companies have had to pivot, refocus and adapt their production lines in order to survive and keep up with customer demands.
These demands require industrial leaders to reset their digital transformation strategies, and I believe cobots (collaborative robots) that are meant to interact closely with humans safely in a shared work space, should play a significant role in these strategies. Cobots are quite different from traditional industrial robots, which work autonomously with safety assured by isolation from human contact. Cobots currently represent a very small percentage of the overall robotics market, but an area I believe will grow rapidly for applications in manufacturing in the next five years. Below are my predictions for why cobots will rise in the industry and how I see industry standards and technology evolving to ensure cobots can stand up to their tasks.
The pandemic is accelerating the adoption of technology that prioritizes safety first and foremost, providing more urgency toward increased digital transformation and automation. A lot of people have got infected in meat packing plants and other such settings—it’s difficult to keep frontline workers six feet apart when they are working on fast-moving production lines, and, on top of that, may need to shout over loud machinery to communicate. These factors create a situation where the virus can easily spread. Cobots can ensure that separation and boundaries on manual handling are able to prevent COVID-19 spread across a number of industrial scenarios.
COVID-19 has also spurred many conversations about the need to reshore US manufacturing in order to prevent our critical supply chains from being concentrated in foreign countries. If COVID creates a return to more manufacturing in the US, technology like automation and cobots will be necessary for companies to compete with developing countries on cost. Cobots can help companies mitigate the full effect of the higher cost of US labor, but also keep active workers in heavily automated environments safe and productive. More robots will be put in manufacturing work and the industry will move toward them having greater capabilities to work alongside and in unison with humans.
Even when we move beyond COVID, we can expect that industrial leaders are going to want to continue to optimize operations through more mature digital transformation. Robots gated off to a specific area have a limit as to how helpful they can be. When you need robots to collaborate on a task such as welding on a car in an automotive plant, moving more freely quickly becomes a requirement for cobots.
For these reasons, cobots are likely to become more popular and prevalent in industrial workplaces. Reaching a point where robots and humans can work very closely together, however, is not without its challenges.
As cobots are placed near humans, safety is of utmost importance, but is also complex. People are unpredictable by nature. We can choose to move an assembly part in a different way than usual, for example. For safety’s sake, robots in close proximity to humans must be able to react without fault to out-of-routine behavior. So, what will it take to get there?
New safety regulations and processes will need to be developed to ensure the market can form successfully without compromising employee safety in industrial settings. On the technology side, equipment must work in a real-time, deterministic way at all times.
I believe the enabling technology elements that will support the future of cobots in industry are a combination of the analysis of data extracted from sensors on the cobots, supported by artificial intelligence (AI) and machine learning, which will feed information immediately into the resulting system and robot’s control. This is what will enable cobots to make decisions that result in a sophisticated combination of learning and collaborative movements that ensure harmonious, safe working operations.
Let’s say the cobot and a human worker are co-moving a product part, for example. It’s the ability to understand which direction a human is moving that part in and immediately adapt to a less predictable move or position that will ensure successful task completion.
How do these enabling technology elements differ from robots today? Robots typically have sensors and cameras that help them relate to their environment and give them the ability to recognize factors they need to handle. But the struggle most people face today is in taking the sensor data and giving sophisticated instructions to robots. Edge computing isn’t a new concept, but I believe the missing link has been the mission-critical edge, and that this will address how cobots can get closer control for real-time implementation of complex decisions in co-working environments.
From a software perspective, the system must also be architected to provide guarantees that a system cannot be reconfigured after boot and that no application can accidentally (or maliciously) cause the robot to fail. The optimum architectures will be mixed criticality systems whereby applications are compartmentalized to ensure that certain applications cannot cause other elements of the system to fail.
The next few years will be full of exciting advancements in the industrial sector in regards to digital transformation. Given the forcing factor that is COVID-19 and the need to make manufacturing in the US competitive, cobots will play a critical role in digital-led industrial business strategies. While robots feel like the safer option in industrial environments today, with the right regulations and technology, cobots can provide the winning edge industrial leaders need for tomorrow.
Source: https://www.smartindustry.com/articles/2020/how-to-capitalize-on-cobots-in-post-covid-industry/